Turbocharger’s welding
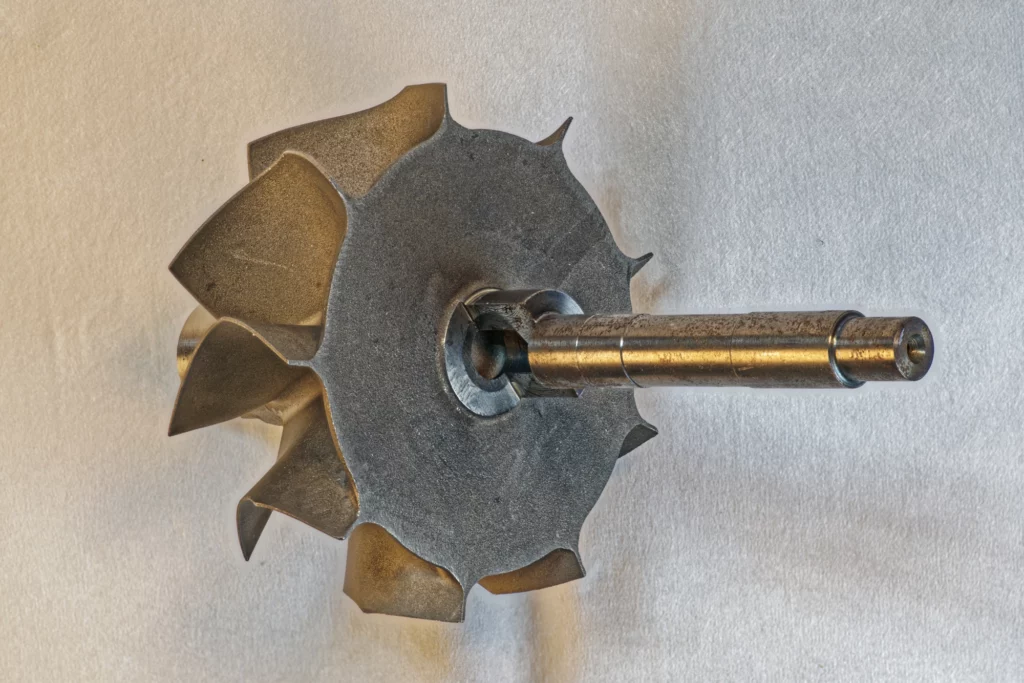
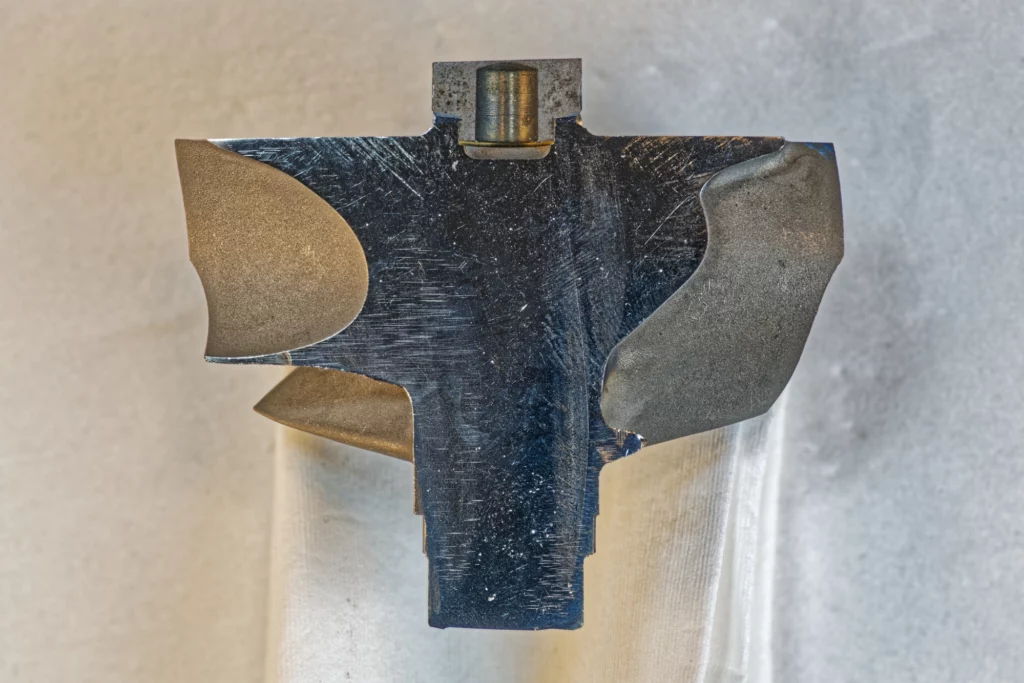
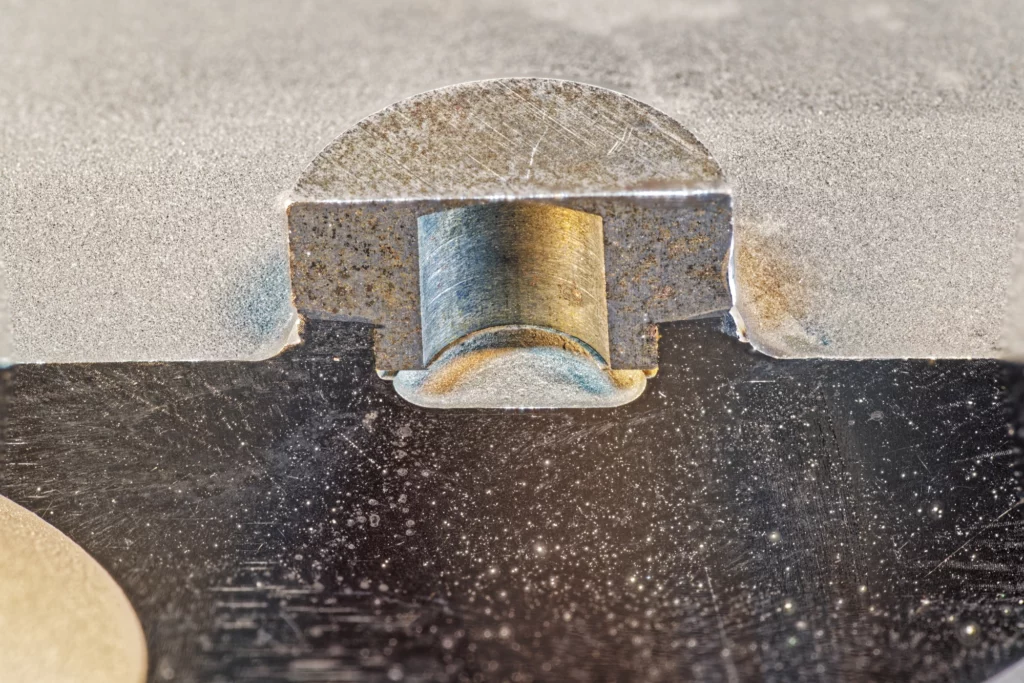
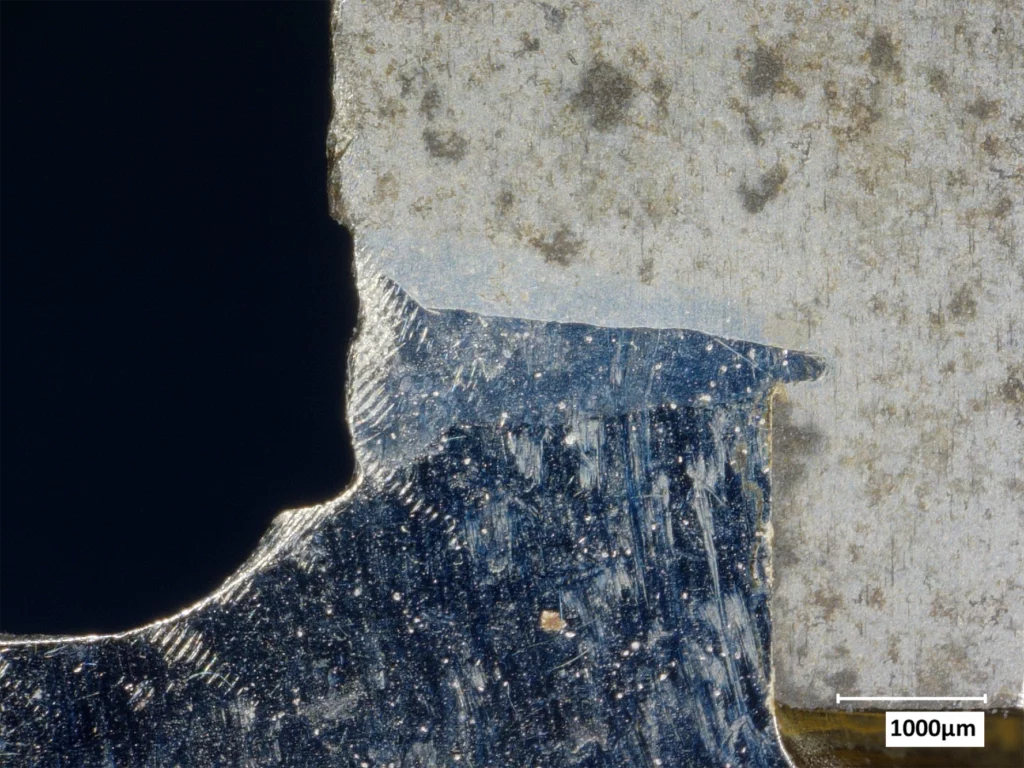
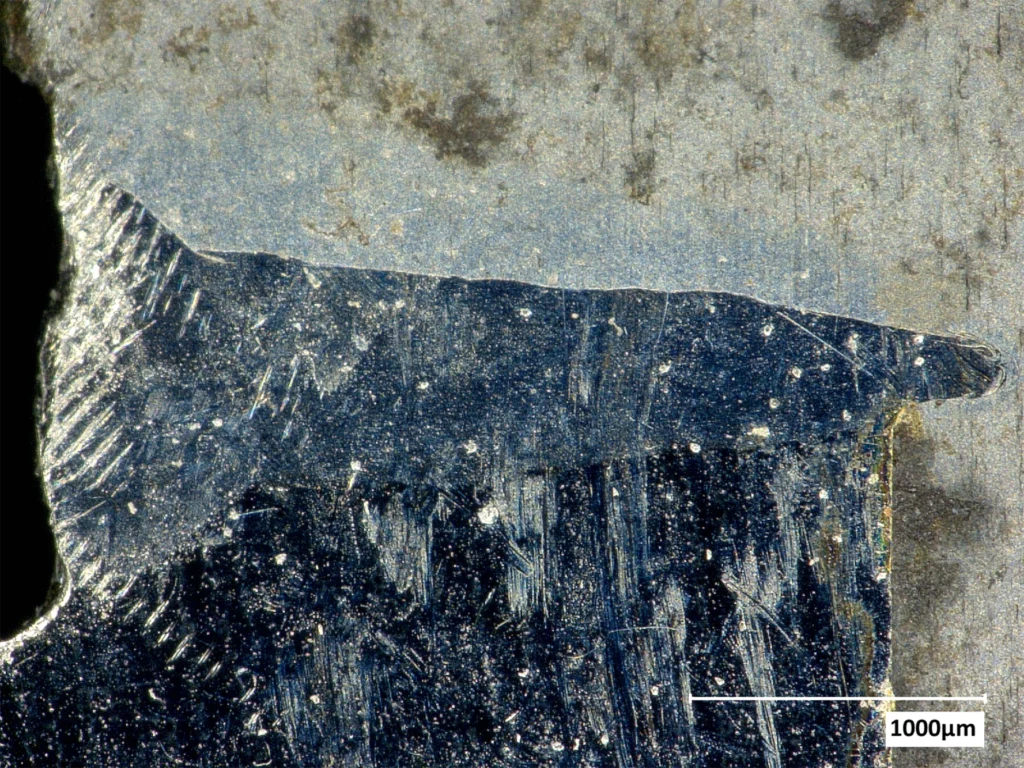
Turbochargers operate under extreme conditions, such as very high temperatures and pressures. Therefore, very strict requirements are placed on manufacturing quality. Various parts of the turbocharger, such as the shaft and the turbine wheel, are typically connected together using electron beam welding. In this way, solid structures with high strength and reliability can be produced.
The vacuum environment and excellent control of the electron beam enable precise welding of two parts with minimal heat affected zone (HAZ) and excellent weld cleanliness. Minimal pore formation, freedom from oxides and high strength – the advantages of electron beam welding are essential for welding turbochargers and enable them to withstand the most extreme loads.