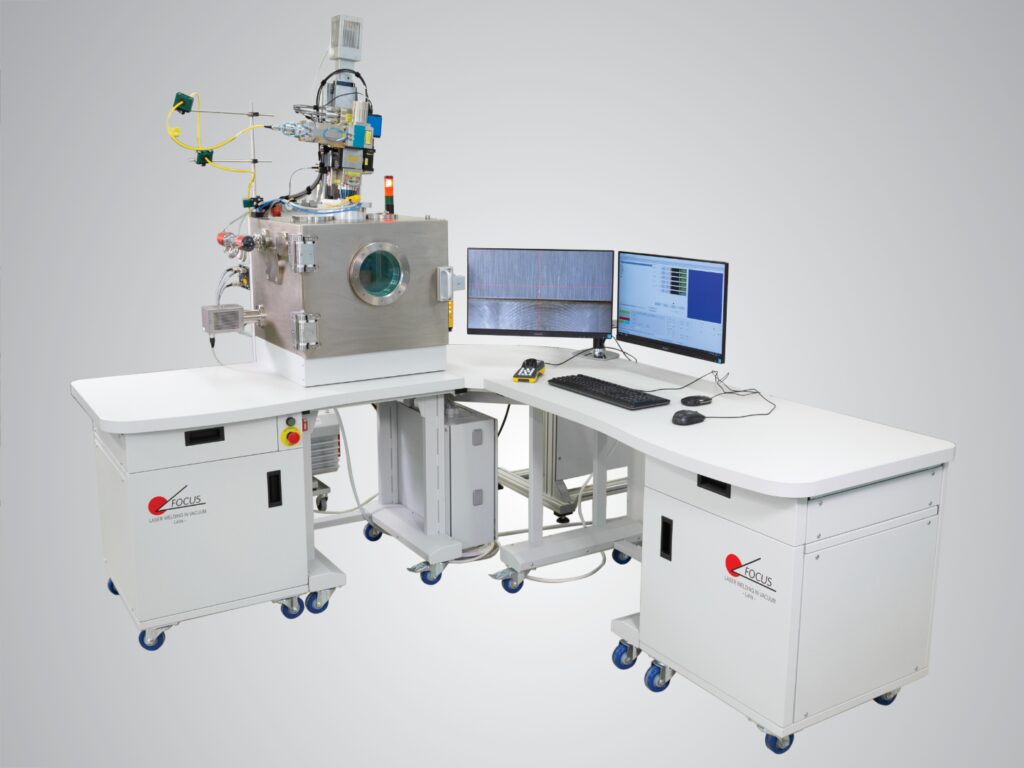
Compact laser in vacuum welding machine with X/Y coordinate table
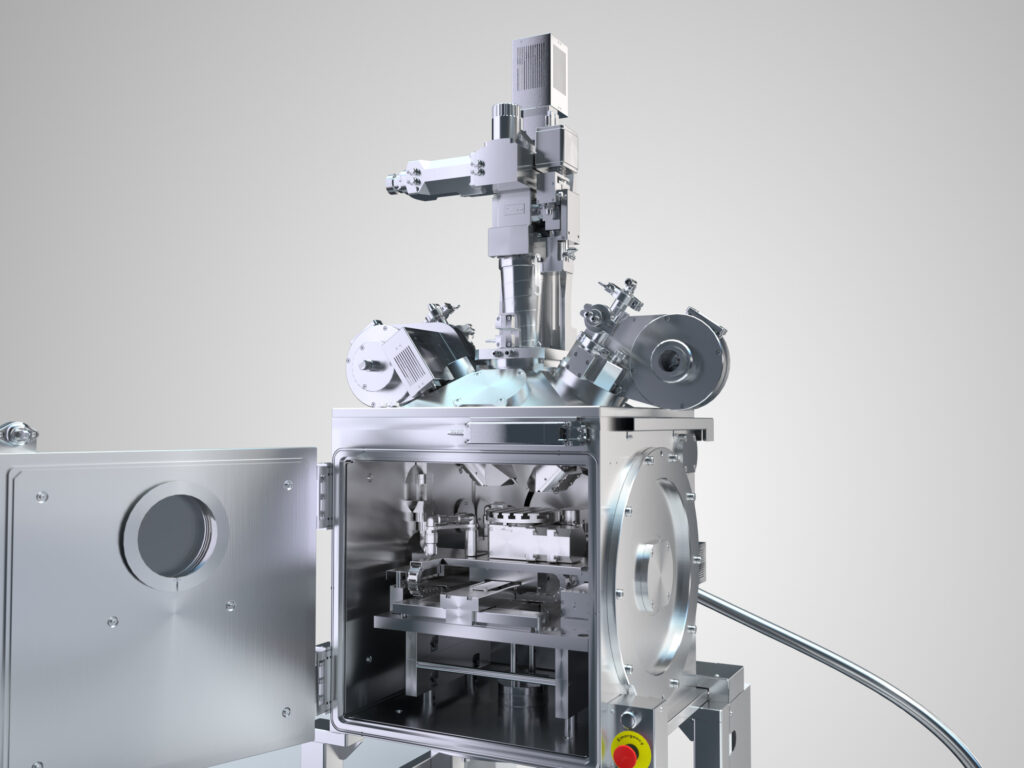
Customized laser in vacuum welding machines with
individual design.
LaVa is the acronym for Laser welding under Vacuum conditions. It´s new technic that combines the well-known benefits of laser welding with those of a low-pressure environment. Welding machine could be equipped with different types of laser in wide power range, adding the vacuum environment allows to get much more stable keyhole without vapor plume and spatter. Wide range of pressure 0.1 and 100 mbar is enough to get impressive results and get at least twice welding depth in comparison to laser welding in atmosphere. Cu, Ti and many more materials can be welded with LaVa on an electron beam welding performance level which now becomes available for magnetic und insulating materials as well.
Vacuum conditions provide much better degassing and allow to avoid the oxidation of the workpiece.
Downloads
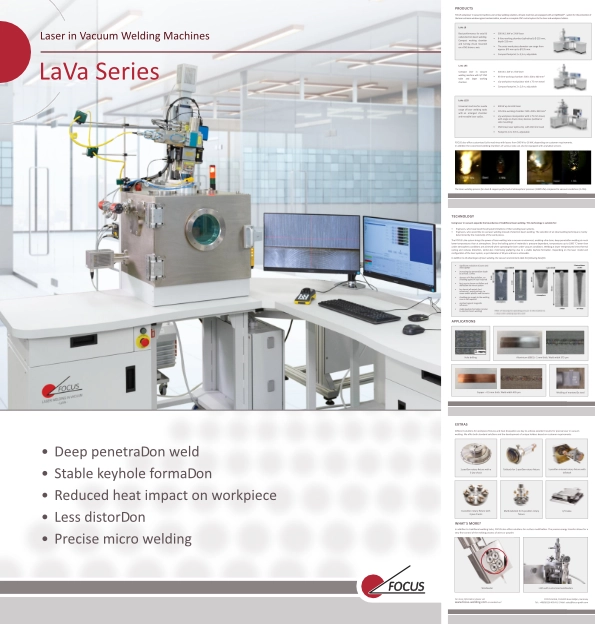
Welding Samples
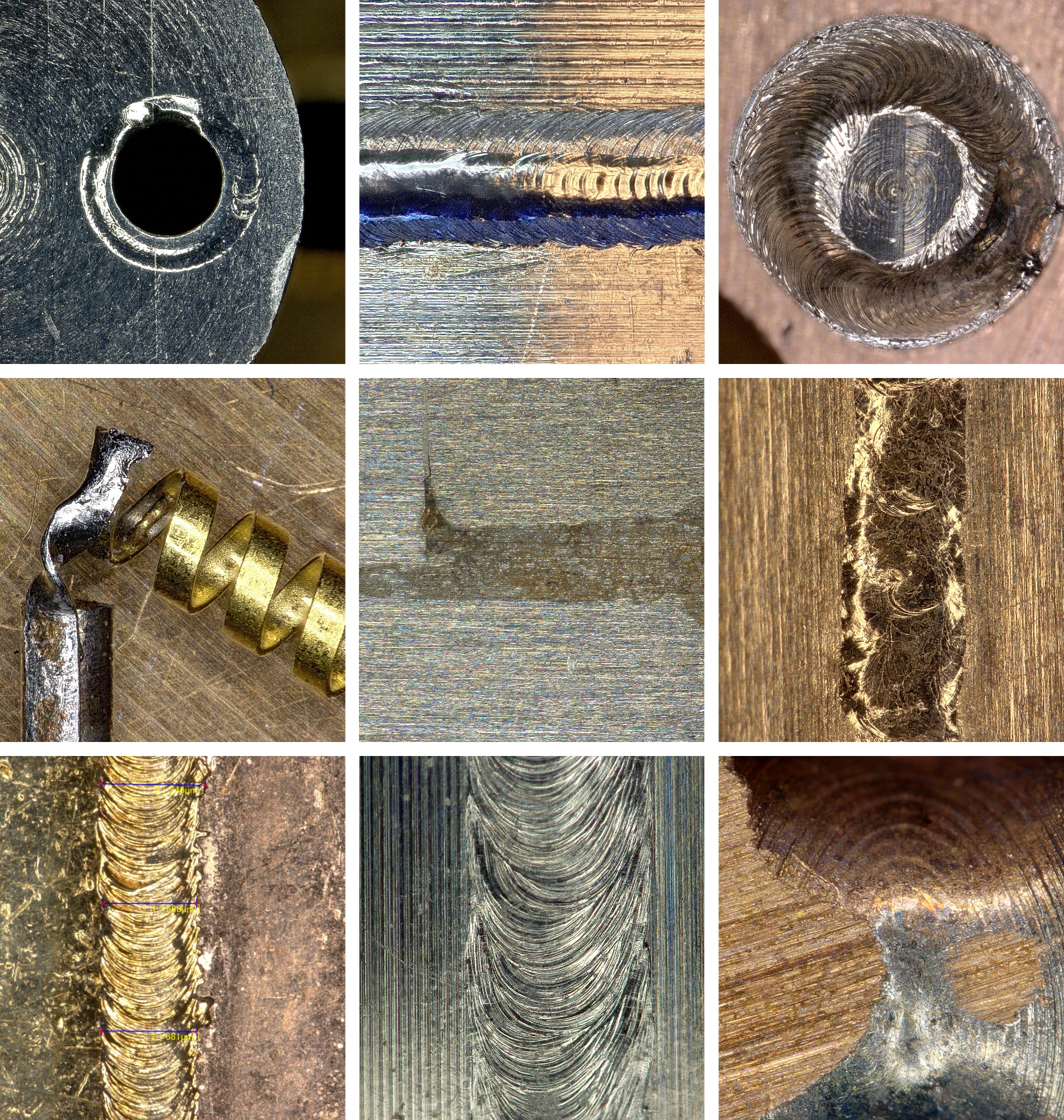
In additional to all advantages of laser welding, welding in vacuum environment get following benefits:
- significant reduction of pores and weld spatter
- increasing the depth penetration at least in 2 times
- improvement of quality of weld joint
- absence of X-Ray sources
- absence of inert gas
- resistance to the effect of magnetism
The two pairs of slow motion video clips are demonstrating the laser welding process for steel & copper performed at atmospheric pressure (1000 hPa) compared to vacuum conditions (1 hPa).
Laser power: 4kW, Welding speed: 0.5m/min, Framerate: 3000 fps
Process advantages at a glance
Combining laser beam and vacuum welding technology not only combines the advantages of both processes, but may also create additional significant benefits.
Laser beam welding in a vacuum sets new standards for the sophisticated welding of demanding and sensitive materials and components.
Welding with a laser beam
- High energy density in the focal position of the laser beam; energy distribution over beam cross-section manipulable with optical elements.
- Thermal welding energy due to absorption of the beam energy in the component (degree of absorption depends on wavelength and material)
- No mechanical stress or vibrations on the component, sensitive electronic components can be welded without problems
- Precise, repeatable and fast positioning of the laser beam via optics or CNC axes
- simple and loss-free guidance of the laser beam from source to welding spot (mirror, light guide, etc.), feed-throughs possible
- high welding depths depending on laser power and feed rate (e.g. steel up to 50mm)
- very low heat-affected zone, especially with pulsed laser beam, reduces stress and crack tendency
Welding in Vacuum
- Adjustment of the vacuum level possible depending on process/material requirements (cost optimization of the pump station)
- pore-free weld seam, as vacuum supports outgassing of the melt
- No unplanned chemical reactions of melt and atmosphere
- no shielding gases required
- no external inclusions in the weld seam
- strength of the weld seam close to the strength of the base material
- enables welding of oxygen affinity or refractory metals (e.g. titanium, tungsten)
- Creation of spatter is reduced (less post processing)
- Process-safe sealing/welding of vacuumed hollow bodies (e.g.sensor housings)
Combination of laser beam and vacuum welding
- Oxygen-affine and refractory metals can be welded with laser beam
- Increase in welding depth achievable with same laser power or lower laser power required
- tendency to pore formation at large welding depths is significantly reduced, homogeneous weld pattern
- Vacuum chamber can simultaneously assume the function of laser protection
- As an alternative to the vacuum, an atmosphere can also be specifically adjusted
- low investment and operating costs compared to available alternative technologies