Electron beam welding (EBW) is used even in such utilitarian areas as heavy automotive industry. In particular, for reliable welding of gearbox parts for trucks, tractors and other vehicles. Gears work under high loads, and the strength of the welds is critical to long-term operation and reliability.
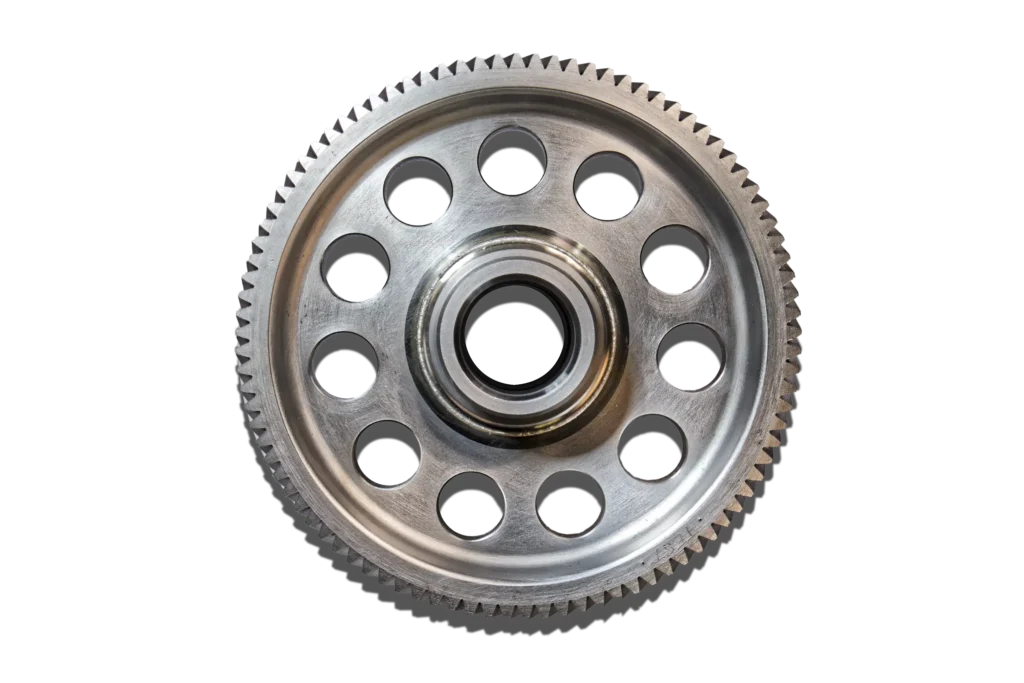
One of the main advantages of EBW in this application is minimizing thermal distortion. In comparison to traditional welding methods, which can strongly heat large areas and deform the material, EBW minimizes the size of the heat affected zone. This precision maintains the original geometry and alignment of the gears, which is critical for smooth operation and efficient transmission of power. Even a small deformation of a gear can cause excessive wear or mechanical errors, so maintaining dimensional accuracy is critical. Materials such as 18CrNiMo7-6, 16MnCr5 and other traditional “automotive” alloys are perfectly welded using electron beam welding. Since EBW is conducted in a vacuum, it prevents the weld zone from being affected by oxygen and other gases. This prevents the formation of oxides and improves the quality of the joint. In addition, because of the minimal heat affected zone among other welding methods, the risk of micro cracks and other defects that can weaken the weld is minimized.
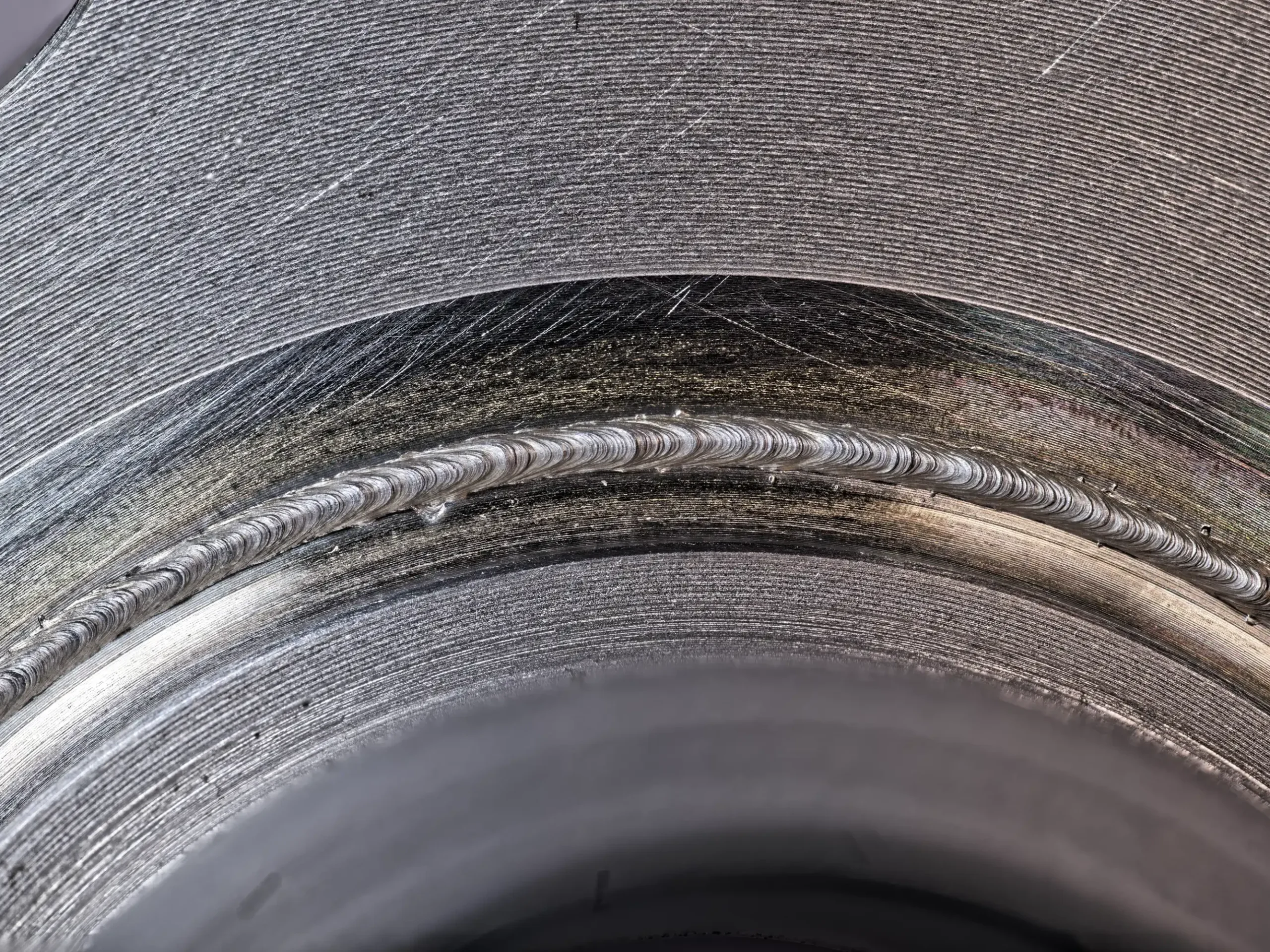
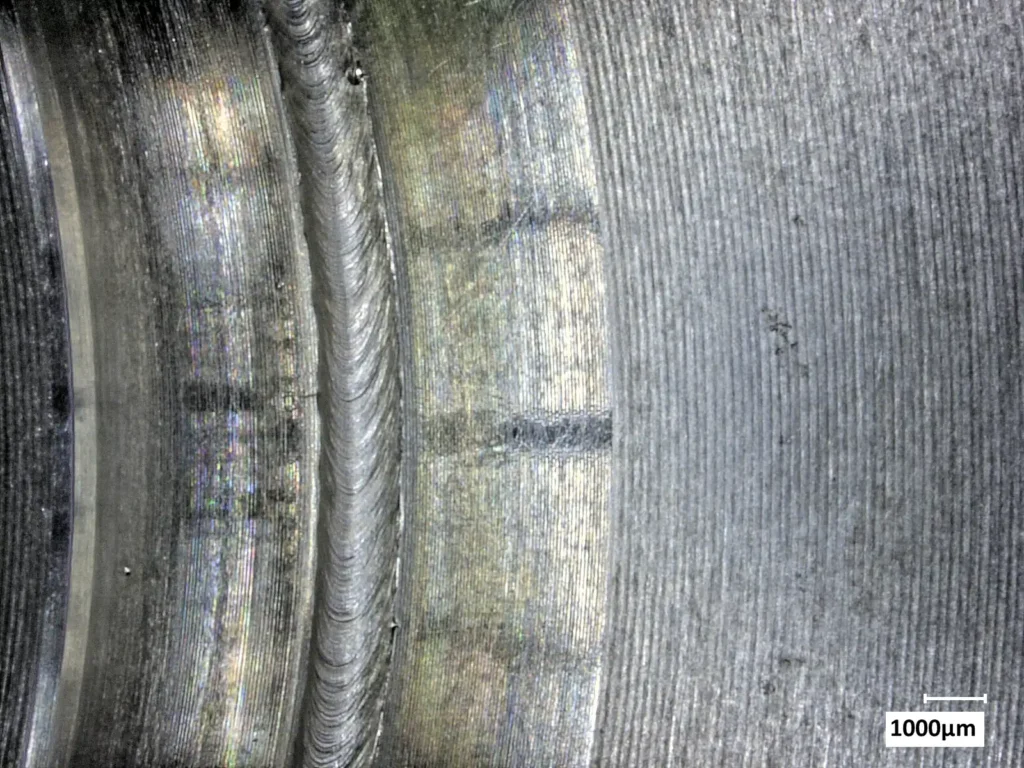
Another significant advantage of EBW is its ability to provide deep penetration. Gears are often of significant thickness and require a welding process that can weld the material at a deep depth without creating cavities or defects. The electron beam welding is the best way to cope with this task, as the power of the electron beam allows even the most delicate areas of the part to be melted smoothly and uniformly. This is especially important for creating durable joints that can bear significant mechanical loads.
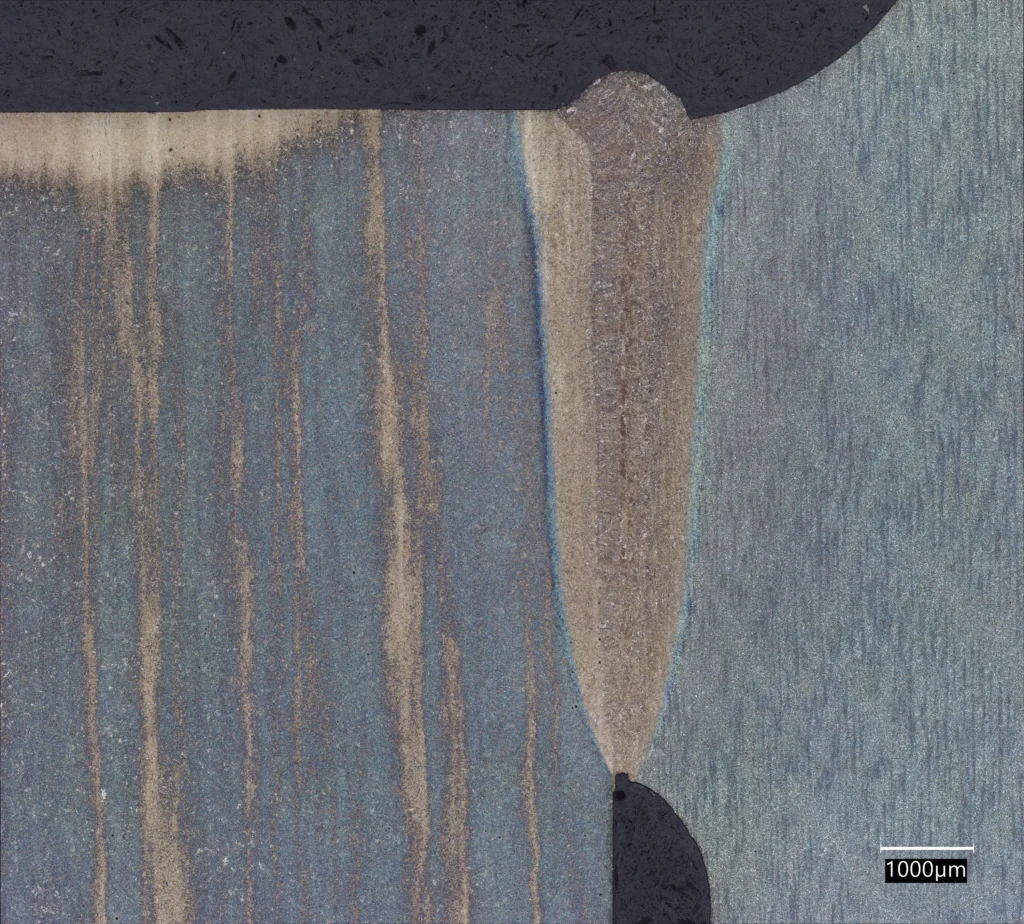
We at FOCUS not only weld parts, but also analyze the weld by destructive and non-destructive testing methods: cut, etch and analyze the seam through a microscope, perform seam inspection with fluorescent dye penetrant testing, CT, hardening test and other methods of analysis.
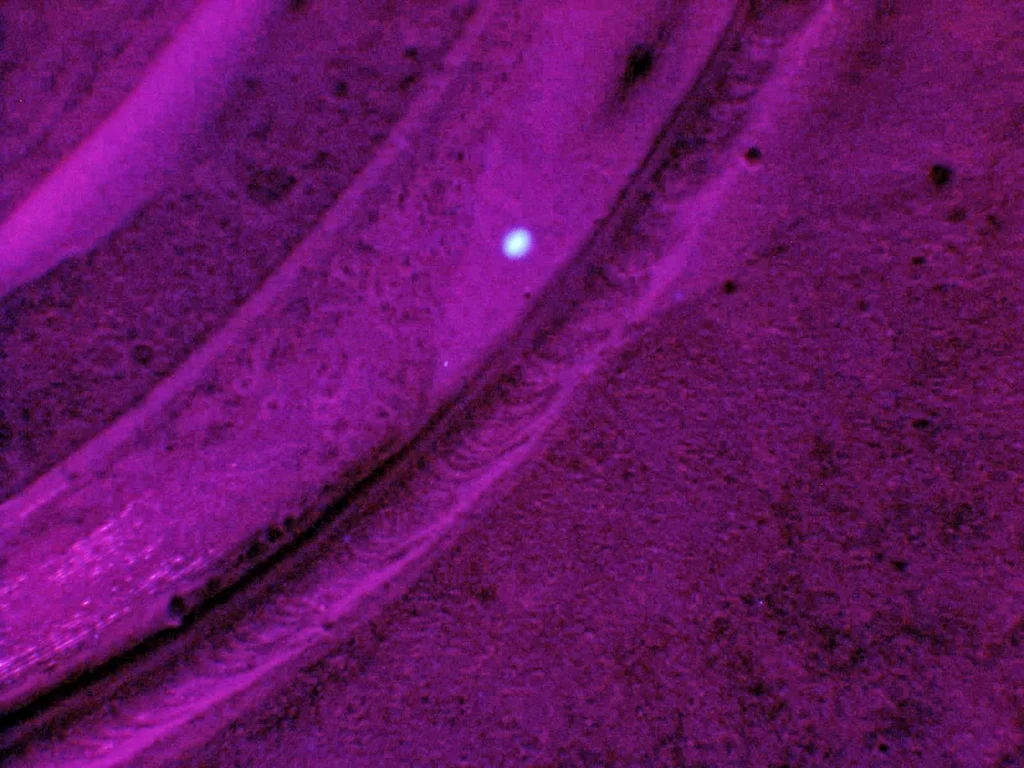
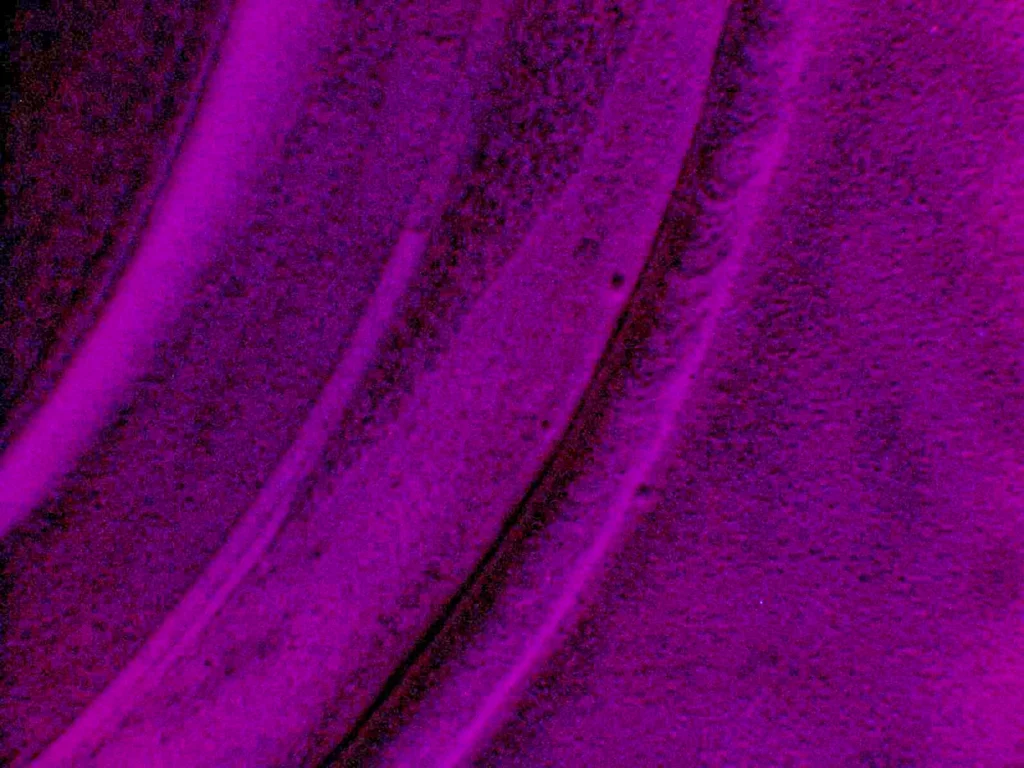
Contact us to discuss your tasks and test weld samples!